Understanding Manifold Valve Working: A Comprehensive Guide
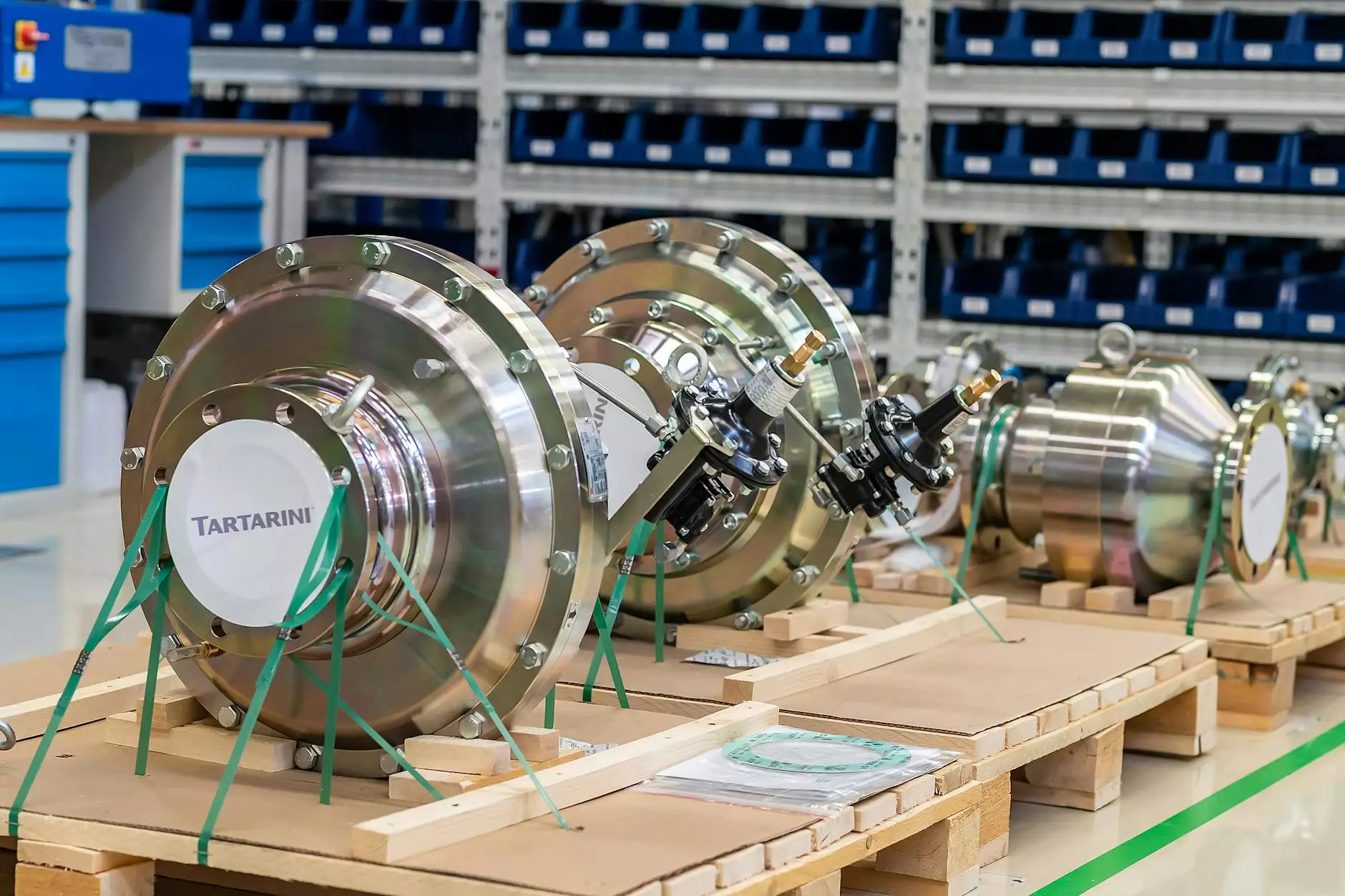
The world of fluid control and management is intricate and essential for various industrial applications. One of the most vital components in this realm is the manifold valve. In this article, we will delve into the manifold valve working principles, their significance in the industry, and the advantages they offer to enhance system efficiency.
What is a Manifold Valve?
A manifold valve is a device that serves as a central point for controlling the flow of fluids in multiple paths. They are widely used in hydraulic and pneumatic systems, enabling a single valve to control several fluid channels simultaneously. This innovative approach simplifies the design of piping systems and reduces the number of required fittings, leading to enhanced system organization and efficiency.
Types of Manifold Valves
- Hydraulic Manifold Valves: Used in hydraulic systems to control the flow and pressure of fluid.
- Pneumatic Manifold Valves: Designed for controlling gases and often used in automated systems.
- Combination Manifold Valves: These integrate both hydraulic and pneumatic services in a single unit.
How Do Manifold Valves Work?
The working principle of manifold valves revolves around controlling fluid flow through a central assembly. Let's break down the process:
1. Fluid Entry and Exit
When fluid enters the manifold valve, it travels through a series of ports that direct the fluid to different outlets based on the valve's configuration.
2. Control Mechanism
Manifold valves can be operated manually or automatically. In manual systems, operators use a lever or knob to change the valve position, whereas automatic systems rely on solenoids or actuators to control flow based on system requirements. This flexibility makes them suitable for various applications.
3. Flow Direction Management
Manifold valves often have several outlets, which allow them to distribute fluid to multiple downstream components. This configuration helps maintain system pressure and ensures that the fluid reaches its destination effectively.
The Importance of Understanding Manifold Valve Working
Grasping the fundamentals of manifold valve working is crucial for several reasons:
- System Efficiency: By utilizing manifold valves, operators can streamline fluid control, reducing energy consumption and enhancing overall system performance.
- Cost-Effectiveness: Fewer fittings and components mean lower material costs and easier maintenance, making them a financially smart choice for industries.
- Reliability: Manifold valves are designed to withstand high pressures and harsh conditions, ensuring reliability in critical applications.
Applications of Manifold Valves
Manifold valves find their utility in numerous industrial applications:
1. Oil and Gas Industry
In the oil and gas sector, manifold valves facilitate efficient control of the flow of hydrocarbons through pipelines, allowing for safe operation in high-pressure environments.
2. Chemical Processing
These valves are integral to chemical processing plants where precise control of fluids is necessary for safety and efficiency.
3. Water Treatment Facilities
Manifold valves help manage the distribution of water and chemicals in treatment plants, ensuring thorough purification processes.
4. Manufacturing
In manufacturing systems, manifold valves are used in assembly lines to direct fluid power tools, enhancing productivity and reducing downtime.
Advantages of Using Manifold Valves
Employing manifold valves comes with numerous benefits:
- Space Saving: A well-designed manifold can consolidate multiple valve functions, saving space in machinery layouts.
- Enhanced Safety: By reducing the number of connections, manifold valves decrease the risk of leaks, ensuring safer operation.
- Improved Maintenance: With fewer components, maintenance tasks become easier and quicker to perform.
Choosing the Right Manifold Valve
When selecting a manifold valve, consider the following factors:
1. Application Needs
Identify the specific fluids that will be used and their properties, including temperature and pressure ranges.
2. Flow Requirements
Calculate the necessary flow rates to ensure that the chosen manifold valve can handle the demands of your system.
3. Control Method
Determine whether manual or automated control is more appropriate for your application, as this will affect the type of valve you select.
4. Material Compatibility
Ensure the material of the manifold valve is compatible with the fluids used to avoid corrosion or degradation.
Conclusion: The Future of Manifold Valves in Industry
As industries continue to evolve and automation becomes increasingly prevalent, the role of manifold valves will undoubtedly expand. Innovations in materials and technology will lead to even more efficient designs, enhancing performance in diverse applications. Understanding manifold valve working is essential for engineers and technicians as they design systems that require reliable fluid control.
By investing in quality manifold valves and ensuring proper installation and maintenance, businesses can significantly increase operational efficiency, reduce costs, and promote safety within their systems. At TechTubes, we are committed to providing high-performance manifold valves and other essential fittings to support your industrial needs.