Understanding Production SLA in Business: A Comprehensive Guide
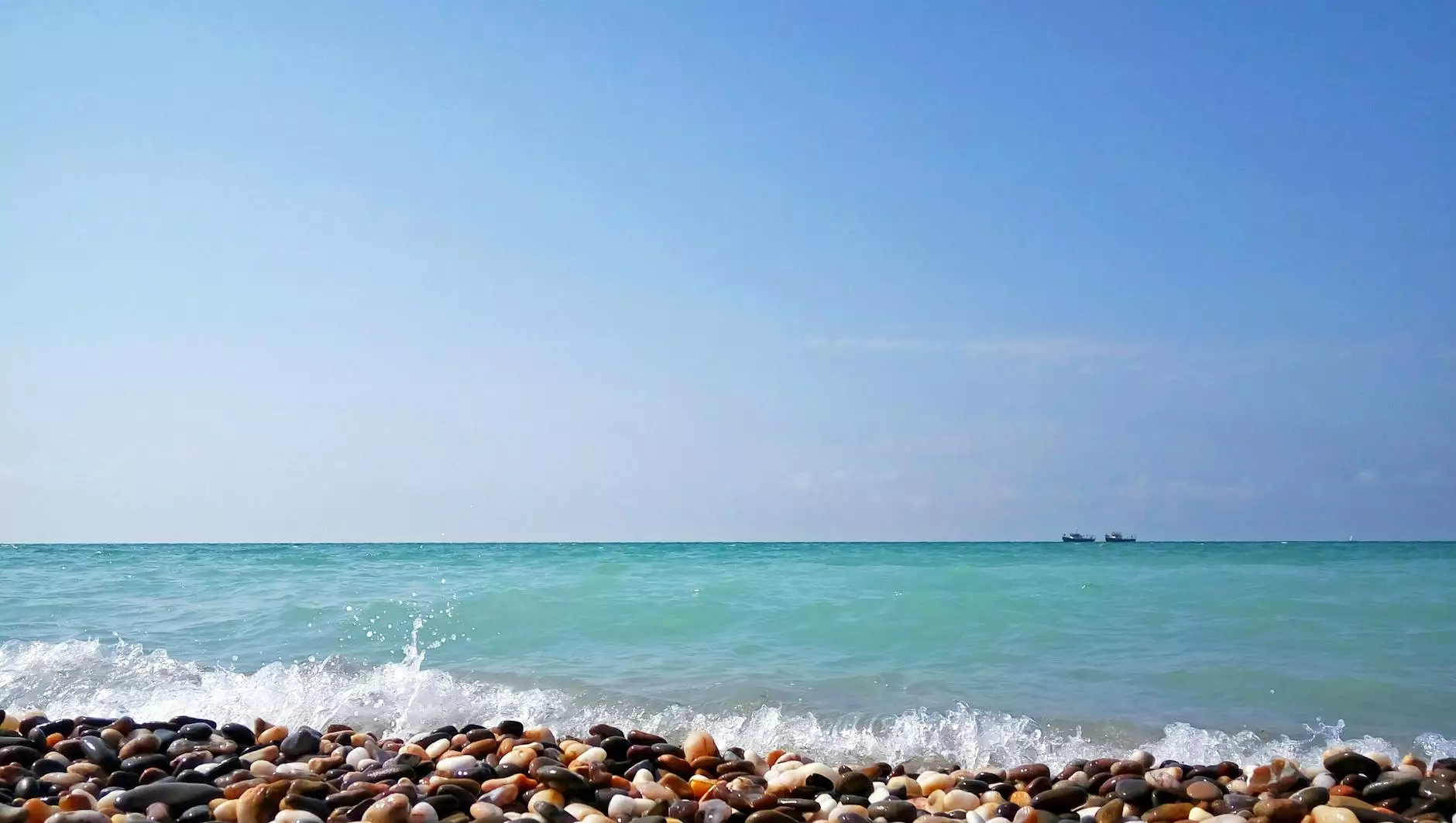
The world of business is constantly evolving, with Production SLA taking center stage in enhancing performance, ensuring quality, and optimizing efficiency across various sectors. Whether you're in the realm of Art Supplies, Product Design, or 3D Printing, understanding and implementing an effective Service Level Agreement (SLA) concerning production can significantly impact your operations and client satisfaction. This article dives deeply into the concept of Production SLA, its importance, benefits, and practical application, ensuring your business strategy remains robust and competitive.
What is Production SLA?
To grasp the significance of Production SLA, one must first understand its components:
- Production: This refers to the complete process of creating goods or services. It includes everything from sourcing materials and manufacturing to final assembly and delivery.
- SLA (Service Level Agreement): This is a formal contractual agreement that articulates the expected level of service from a provider in relation to its clients. It sets clear benchmarks for performance and accountability.
Essentially, a Production SLA outlines the expectations regarding production performance, quality standards, timelines, and the responsibilities of each party involved in the production process.
Importance of Production SLA in Business
The role of a well-defined Production SLA in your business landscape cannot be overstated. Here are several pivotal reasons why integrating a robust SLA into your production workflow is essential:
1. Clarity and Transparency
One of the principal benefits of a Production SLA is the introduction of clarity and transparency in the production process. When all parties understand their roles and responsibilities, it sets the stage for a smooth and efficient working relationship.
2. Performance Measurement
SLAs provide benchmarks that allow businesses to measure their performance against predefined metrics. This aspect is crucial in identifying areas that need improvement, ensuring that production meets the standards expected by stakeholders.
3. Risk Management
By establishing clear expectations, a Production SLA helps mitigate risks associated with production delays, quality issues, and miscommunication. It serves as a documented reference point in case of disputes, fostering a sense of accountability.
4. Enhanced Customer Satisfaction
With a focus on delivering quality and timely services, businesses that employ effective SLAs are better positioned to satisfy customer expectations. This can lead to improved customer loyalty, repeat business, and positive word-of-mouth referrals.
5. Improved Resource Management
Proper SLAs aid in optimizing resource allocation, ensuring that the right resources are available at the right times during the production cycle. This efficiency can lead to cost savings and better overall performance.
Creating an Effective Production SLA
Crafting an effective Production SLA involves several crucial steps. Below, we outline a concise guide to creating a comprehensive SLA tailored for your business needs:
1. Identify Key Stakeholders
Begin by identifying all key stakeholders involved in the production process. This includes internal teams, suppliers, and any third-party services, ensuring everyone’s roles are recognized.
2. Define Scope and Objectives
Clearly outline the scope of the SLA, detailing what aspects of production it covers. Set objectives that align with your business goals, ensuring they are both measurable and achievable.
3. Establish Performance Metrics
Determine the performance metrics that will be used to assess production efficiency, quality, and timeliness. Metrics could include:
- Turnaround times
- Production yield rates
- Defect rates
- Service availability
4. Set Service Level Objectives (SLOs)
Based on the agreed metrics, establish Service Level Objectives that articulate the expected performance levels. For example, you may decide on a 98% defect-free rate in supplied materials or a 24-hour turnaround for prototypes in Product Design.
5. Document Everything
Ensure all the discussions, agreements, and expectations are documented. A formal, written SLA is vital for clarity and avoids any misunderstandings.
6. Review and Revise Regularly
Lastly, treat the SLA as a living document. Regular reviews and revisions ensure that the agreement remains relevant and adapts to any changes in your business environment or market conditions.
Best Practices for Implementing Production SLA
Now that you have a foundational understanding of Production SLA, it's essential to know how to implement it effectively in your organization. Here are some best practices to consider:
1. Foster Communication
Effective communication is fundamental to successful SLA implementation. Establish regular meetings with all stakeholders to discuss progress, challenges, and gather feedback.
2. Utilize Technology
Leverage technology and tools to monitor production processes against SLA metrics. Tools like project management software and performance dashboards can offer valuable insights and facilitate better decision-making.
3. Provide Training
Invest in training for your teams regarding the SLA’s importance and their roles in upholding it. A knowledgeable team is better equipped to achieve the set goals.
4. Encourage Accountability
To further enhance the efficacy of your Production SLA, promote a culture of accountability within your team. Everyone should understand their responsibilities and how they impact overall service delivery.
Case Studies: Successful Production SLA Implementation
Examining real-world examples can offer deeper insights into the successful application of Production SLA. Consider the following industries:
Art Supplies Industry
An art supplies company implemented a Production SLA with its suppliers that outlined clear production timelines for restocking materials, quality specifications, and delivery expectations. As a result, their inventory management became more streamlined, leading to a 20% reduction in stockouts and enhanced customer satisfaction. The clear metrics of their SLA allowed them to assess supplier performance regularly, addressing issues proactively.
Product Design Sector
A product design firm adopted a strict Production SLA with its manufacturing partners, defining specific timelines for prototypes and iterations. This structured approach enabled the firm to reduce prototype delivery times by 35%, allowing for quicker market entry and increased client engagement. The metrics set within their SLA ensured a high quality of prototypes, directly enhancing their reputation.
3D Printing Business
In a 3D printing business, a comprehensive Production SLA was established with its clients. This agreement defined turnaround times for printed models, quality checks, and revision rounds. As a result, the firm was able to achieve a 98% on-time delivery rate, significantly boosting customer trust and loyalty. The SLA served as a foundation for comparing performance metrics and improving operational efficiency.
The Future of Production SLA
As businesses continue to evolve and adapt to new challenges, the role of Production SLA is likely to become even more critical. Innovations in technology, shifts toward sustainability, and an increased focus on service quality will shape how production agreements are structured and monitored.
1. Technological Advancements
The rise of Industry 4.0, with its emphasis on automation and data exchange, will influence SLAs. Technologies like IoT (Internet of Things) can provide real-time data on production processes, enabling more dynamic and responsive SLAs.
2. Sustainability Considerations
Increasing awareness around sustainability will likely impact the metrics included in Production SLA. Businesses may start to include sustainability goals, such as waste reduction and energy efficiency, within their SLAs.
3. Client-Centric Approaches
With the growing importance of customer experience, SLAs may shift focus to align with client-centric metrics, ensuring that businesses are not only meeting production goals but also prioritizing client satisfaction.
Conclusion
In conclusion, an effective Production SLA is not just a contractual obligation; it is a powerful tool for enhancing business processes across sectors such as Art Supplies, Product Design, and 3D Printing. By establishing clear expectations, measuring performance, and continuously refining these agreements, businesses can foster accountability, improve customer satisfaction, and drive operational excellence. As the landscape of production continues to change, embracing SLAs as a strategic component will undoubtedly position businesses like yours on the path to long-term success.
For more valuable insights into managing production and service agreements, be sure to explore additional resources and data tailored for your specific industry needs at arti90.com.