The Advantages of Low Pressure Casting in Modern Manufacturing
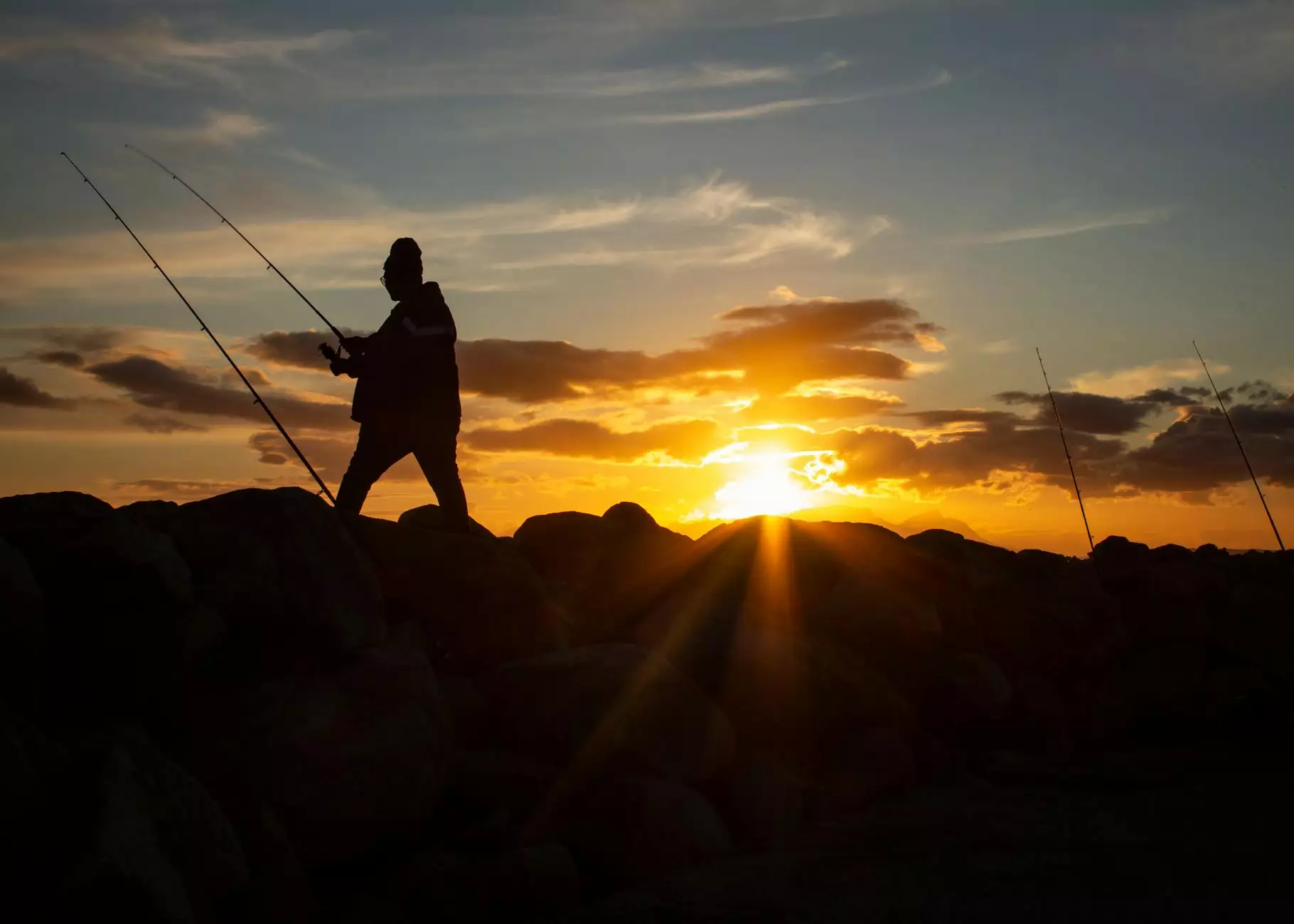
In today’s competitive market, businesses are continuously seeking innovative methods to improve product quality and manufacturing efficiency. One such method is low pressure casting, a technique that has garnered significant attention for its ability to produce high-quality metal components with exceptional precision. In this comprehensive article, we will delve into the intricacies of this casting technique, its applications, benefits, and how it aligns with the domains of art supplies, product design, and 3D printing.
Understanding Low Pressure Casting
Low pressure casting is a manufacturing process that involves pouring molten metal into a mold under low pressure, typically ranging from 1 to 3 bars. This method is characterized by its ability to create complex shapes with smooth finishes, making it a preferred choice in various industries, including automotive, aerospace, and consumer goods.
The Process of Low Pressure Casting
The low pressure casting process can be summarized in several key steps:
- Preparation of the Mold: A mold is created from high-quality materials that can withstand the pressures and temperatures involved in the casting process.
- Melting the Metal: The chosen metal, often aluminum or magnesium alloys, is heated in a furnace until it reaches a molten state.
- Applying Pressure: Once the metal is molten, it is introduced into the mold. Low pressure is applied, ensuring that the molten metal fills the mold uniformly and eliminates trapped air, which can lead to defects.
- Cooling and Solidifying: The metal is allowed to cool and solidify within the mold, forming the final product.
- Finishing: After solidification, the mold is removed, and further finishing processes, such as machining or surface treatments, may be applied to achieve the desired specifications.
Benefits of Low Pressure Casting
The advantages of utilizing low pressure casting are numerous, making it a viable choice for many manufacturers.
1. Enhanced Product Quality
One of the most significant benefits of low pressure casting is the superior quality of the finished products. The low-pressure application allows for:
- Improved Surface Finish: The smooth surface finish reduces the need for extensive post-processing.
- Better Dimensional Accuracy: Low pressure ensures that the molten metal fills every part of the mold, resulting in precise dimensions.
- Reduced Porosity: By effectively eliminating trapped air and gases, this method significantly decreases the likelihood of porosity, leading to stronger final products.
2. Cost Efficiency
Businesses are always looking to minimize costs while maximizing output, and low pressure casting serves this purpose effectively:
- Lower Production Costs: The efficiency of the process leads to a reduction in material waste and energy consumption.
- High Production Rates: The ability to produce large quantities quickly can significantly decrease overall manufacturing time.
3. Versatility in Application
Another remarkable aspect of low pressure casting is its versatility. This technique can be used with a variety of metals and alloys, allowing manufacturers to select the best material for their specific application. Applications include:
- Automotive parts such as engine components
- Aerospace components where lightweight but strong materials are crucial
- Consumer goods, including appliances and electronics
4. Environmental Considerations
In an era where environmental sustainability is paramount, low pressure casting shines as a greener manufacturing option. With lower energy requirements and reduced waste, manufacturers can demonstrate a commitment to eco-friendly practices.
Low Pressure Casting and Product Design
In the realm of product design, low pressure casting opens new avenues for creativity and innovation. Designers can take advantage of the following:
1. Complex Geometries
The pressure dynamics of this process allow for the creation of intricate designs that would be impossible or economically unfeasible with other methods. This capability encourages designers to explore new shapes and functionalities.
2. Material Selection
The ability to cast with various metals means designers can choose materials that best fit their product requirements, enhancing functionality and aesthetic value.
Integrating Low Pressure Casting with 3D Printing
The combination of low pressure casting and 3D printing brings forth a revolutionary approach to manufacturing and design:
1. Rapid Prototyping
Utilizing 3D printing for mold creation allows designers to quickly prototype their products, enabling faster iterations and adjustments based on testing results.
2. Customization
Custom designs can be implemented without significant cost increases, offering businesses the flexibility to cater to specific customer needs and preferences.
Challenges and Considerations
Despite the numerous benefits, low pressure casting does come with its challenges. Businesses must consider:
- Initial Setup Costs: While operational costs may decrease, the initial investment in specialized equipment can be considerable.
- Technical Expertise: The process requires skilled personnel who understand the intricacies of metal forming and mold design.
- Material Limitations: Certain alloys may not be feasible for low pressure casting, requiring additional consideration during the design phase.
Conclusion
In conclusion, low pressure casting presents a myriad of advantages for businesses in modern manufacturing. Its ability to produce high-quality products efficiently and sustainably makes it an ideal choice for various industries, particularly in the fields of art supplies, product design, and 3D printing. As companies strive to innovate and improve their processes, embracing low pressure casting can lead to enhanced product quality, reduced production costs, and greater design flexibility.
By understanding the processes, benefits, and potential challenges associated with low pressure casting, businesses can better position themselves to leverage this technology for superior product outcomes and competitive advantage. As the manufacturing landscape continues to evolve, adopting such advanced techniques will undoubtedly be crucial for sustained growth and success.